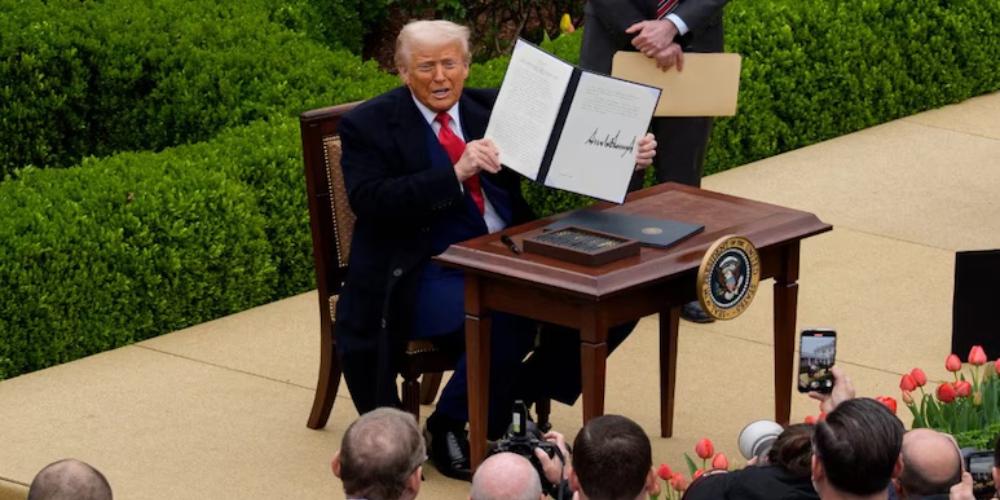
The Truth Behind Tariffs and Their Effect on Blue-Collar Employment
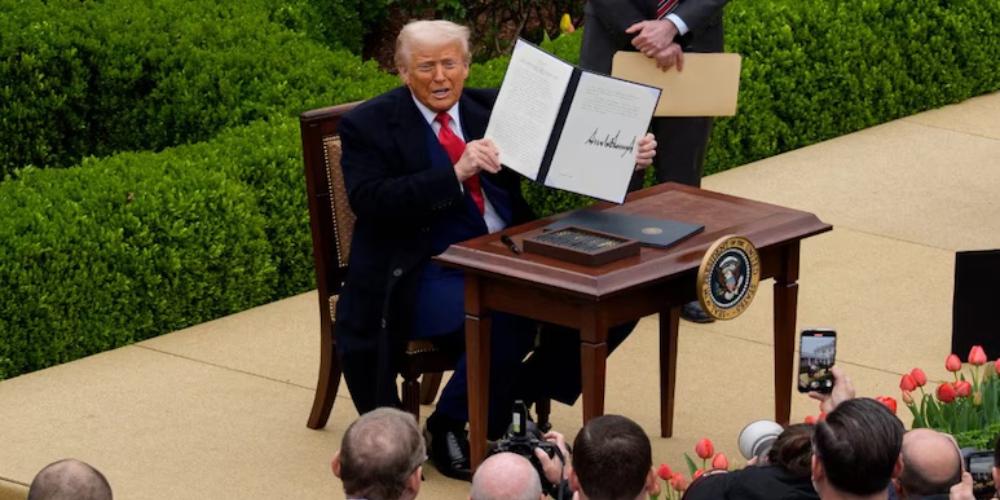
More in Labor law
-
`
Inside the Duterte Family’s Desperate Quest for Power in 2025 Elections
As the Philippines gears up for the 2025 elections, the Duterte family is once again positioning itself for a significant role...
October 5, 2024 -
`
Here’s Everything You Need to Know About Divorce Finances & Procedures
Divorce is never easy. And when you add finances to the mix, it can feel even more overwhelming. Understanding how divorce...
September 27, 2024 -
`
Is the Murdoch Family Succession a Family Secret Kept Under Wraps?
In a surprising turn of events, the Murdoch family succession has become the subject of intense legal scrutiny. A group of...
September 21, 2024 -
`
Did Melania Trump File for Divorce?
Recently, the internet was abuzz with speculation: Did Melania Trump file for divorce from Donald Trump? The rumor spread like wildfire,...
September 11, 2024 -
`
Gambling Laws in California: What is Legal & What Isn’t?
Is online gambling legal in California? This is a question that many residents and visitors of the Golden State ask as...
September 6, 2024 -
`
What Are Legal Margins for a Letter? Crafting a Professional Legal Letter
Writing a professional legal letter requires careful consideration of various elements to ensure clarity, precision, and effectiveness. One crucial aspect to...
August 29, 2024 -
`
How to Remove Someone From Your Family Tree
Managing a family tree can be a fulfilling journey, but sometimes, there is a need to remove certain profiles. Whether the...
August 24, 2024 -
`
Why Did Yolanda and David Frost Divorce?
Why did Yolanda and David Frost divorce? This question has lingered in the minds of many, given their seemingly perfect union....
August 12, 2024 -
`
Can You Go to Jail for Not Paying Child Support? Here’s What Happens
Can you go to jail for not paying child support? Failure to pay child support can have severe consequences, including the...
August 9, 2024
You must be logged in to post a comment Login